PRODUCTS
Categories
Hot Products
Conveyor Wear Plates
Leave a request and we will contact you within 10 minutes!
PRODUCT INTRODUCTION
Conveyor wear plates are components used in conveyor systems to resist wear , and prolong the service life of the equipment.
Function
Reduce Wear: The primary function is to reduce the wear of conveyor components. By installing wear plates on parts like chutes, hoppers, and conveyor belts, the direct contact between the conveyed materials and the equipment is reduced, thereby protecting the equipment and prolonging its service life123.
Improve Conveying Efficiency: Wear plates with good self-lubrication, such as those made of UHMWPE, can reduce the friction coefficient between the materials and the conveyor, making the materials move more smoothly and improving the conveying efficiency3.
Enhance Equipment Stability: By reducing wear and tear and the occurrence of failures, wear plates help to maintain the stable operation of the conveyor system, reducing the frequency of equipment shutdown for maintenance and improving the overall production efficiency.
WHERE IS IT USED
Conveyor wear plates have a wide range of applications in various industries due to their ability to reduce wear and improve the efficiency and durability of conveyor systems. Some of the main applications are as follows:
Mining Industry
Ore Conveying: In mines, conveyor wear plates are used in chutes and conveyors that transport ores. The high-hardness wear plates can withstand the abrasion of rough ore particles, preventing the rapid wear of conveyor components and ensuring the efficient transportation of ores from the mining area to the processing plant.
Coal Handling: For coal mines, wear plates are installed on conveyor belts and transfer points to resist the wear caused by the continuous movement of coal. They help to maintain the integrity of the conveyor system and reduce the frequency of equipment maintenance, thereby improving coal mining and transportation efficiency.
Construction Industry
Aggregate Processing: In sand and gravel processing plants, conveyor wear plates are used in conveyors that transport aggregates such as sand, gravel, and crushed stone. The wear plates protect the conveyor equipment from the abrasive action of these materials, ensuring the stable operation of the production line and reducing equipment downtime.
Concrete Batching Plants: Wear plates are also applied in concrete batching plants to protect the conveyors that transport cement, aggregates, and other raw materials. They help to maintain the accuracy of material dosing and improve the overall efficiency of concrete production.
Power Industry
Coal Feeding Systems: In power plants, conveyor wear plates are crucial in coal feeding systems. They are installed on coal conveyors to prevent excessive wear of the conveyor belts and components caused by the continuous transportation of coal, ensuring the stable supply of coal for power generation.
Ash and Slag Handling: Wear plates are used in conveyors that handle ash and slag discharged from boilers. The high-temperature and abrasive resistance of wear plates enable them to withstand the harsh conditions of ash and slag transportation, protecting the conveyor equipment and reducing maintenance costs.
Chemical Industry
Powder and Granular Material Conveying: In chemical plants, conveyor wear plates are used to transport various powder and granular materials, such as chemical fertilizers, resins, and pigments. The wear plates not only resist wear but also prevent material leakage and contamination, ensuring the safe and efficient operation of the production process.
Corrosive Material Handling: For the transportation of corrosive materials, wear plates made of corrosion-resistant materials such as ceramics and special plastics are used. These wear plates can withstand the corrosion of chemical substances and maintain the performance of the conveyor system.
PRODUCT DESIGN
1、Material Selection
- Based on Working Environment: For harsh conditions with high abrasion and impact in mining and construction, high-hardness alloy steel or high-chromium white iron is used. In the food and beverage industry requiring hygiene and low friction, food-grade UHMWPE is preferred. In corrosive chemical environments, ceramic or corrosion-resistant plastic wear plates are suitable.
- Considering Cost and Performance: Metal wear plates are cost-effective with good overall performance. Ceramic wear plates have excellent wear resistance but are more expensive and brittle. Plastic wear plates are relatively inexpensive, lightweight, and have good self-lubrication.
2、Thickness Design
- According to Wear Intensity: In areas with high wear intensity, such as where large, rough materials are conveyed, thicker wear plates of 10 - 50 mm may be used. For light-duty conveying of small, light materials, thinner plates of 3 - 10 mm can suffice.
- Considering Equipment Load: The thickness should be selected considering the load-bearing capacity of the conveyor equipment to avoid excessive load caused by overly thick plates affecting the normal operation of the conveyor.
3、Shape and Size Design
- Matched to Conveyor Components: The shape and size of wear plates should match the conveyor components, such as being designed as rectangular, circular, or custom-shaped to fit chutes, hoppers, and conveyor belts.
Allowing for Installation and Replacement: The design should consider easy installation and replacement, with appropriate holes, grooves, or connection methods for convenient fixing to the conveyor equipment.
THE CONVEYOR BELT HAS THE FOLLOWING DESIGN
1 Single-Layer Structure: Some simple conveyor wear plates have a single-layer structure, which is usually made of a single material with uniform performance throughout. For example, some plastic wear plates are made entirely of UHMWPE, which has good overall wear resistance and self-lubrication.
2 Composite Structure: Many wear plates adopt a composite structure for better performance. For instance, some metal-ceramic composite wear plates combine the high strength and toughness of metal with the high hardness and wear resistance of ceramics. The metal layer provides the base support and impact resistance, while the ceramic layer on the surface resists wear. Another example is the combination of a metal substrate and a plastic coating. The metal substrate ensures the strength of the wear plate, and the plastic coating provides good wear resistance and self-lubrication.
TABLE OF TECHNICAL CHARACTERISTICS
FEATURES AND BENEFITS
1. Three Decades of Expertise
Established in 1994, we bring 30+ years of specialized experience in bulk material handling equipment manufacturing and system integration, ensuring deep industry insights and technical mastery.
2. Robust China-Based Supply Chain
Leverage our vertically integrated supply network with long-term partnerships with certified Chinese steel mills, foundries, and component suppliers, guaranteeing cost efficiency, quality consistency, and on-time delivery.
3. Financial Strength & Flexible Terms
Backed by solid financial reserves, we offer tailored payment solutions for cyclical procurement (e.g., staggered payments, L/C flexibility) to optimize clients’ cash flow management.
4. Risk-Mitigated Operations
Proactive risk control frameworks minimize contractual, quality, and delivery risks: ISO 9001-certified quality assurance protocols Dual-source procurement strategies for critical components Escrow-backed performance guarantees
5. End-to-End Customization
Deliver turnkey solutions spanning design, fabrication, automation integration, and lifecycle support, tailored to site-specific requirements (e.g., extreme climates, hazardous zones).
6. After-Sales Excellence
24/7 multilingual technical support and a global spare parts network ensure <12-hour response times for critical breakdowns.
INSTALLATION AND COMMISSIONING FROM PROFESSIONALS
JUXIN also provides services for the installation and commissioning of conveyor equipment. Our team of experienced specialists will efficiently set up the operation of the conveyor line at your enterprise in a timely manner. We also offer installation supervision, where our specialist will visit your facility after equipment delivery to oversee the installation and launch process carried out by your personnel.
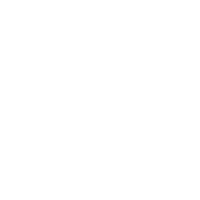
PRE-SALES:EQUIPMENT SELECTION
Assisting customers in selecting the most suitable belt conveyor for their specific needs and requirements. Additionally, we offer technical advice and guidance to facilitate informed decision-making on bulk material handling equipment. Furthermore, we can provide the following information:
• Customized solutions and design services
• Delivery lead time
• Equipment operation and maintenance
• Environmental and safety measures
• Integration with existing equipment
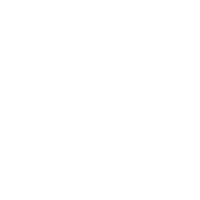
AFTER-SALES: 24/7 HOTLINE SUPPORT
We have established a hotline (+86 18622502901) to promptly address customer inquiries, feedback, and complaints. Our support is available 24 hours a day, seven days a week. Generally, our engineers will work remotely to resolve your issues.
- We provide training for customers on effective and safe operation and maintenance of the belt conveyor.
- We offer technical support and troubleshooting assistance to address any operational issues or concerns with the belt conveyor.
- We supply spare parts and components as needed, ensuring prompt delivery and compatibility with the specific belt conveyor model.
FILL OUT THE QUESTIONNAIRE
Have you filled out the questionnaire?
You need to fill out the questionnaire and send it to our mailbox
Our experts will calculate the mobile belt conveyor and provide the price.
Questionnaire download
If you encounter any problems while filling out the questionnaire, you can call us:
PHOTO GALLERY
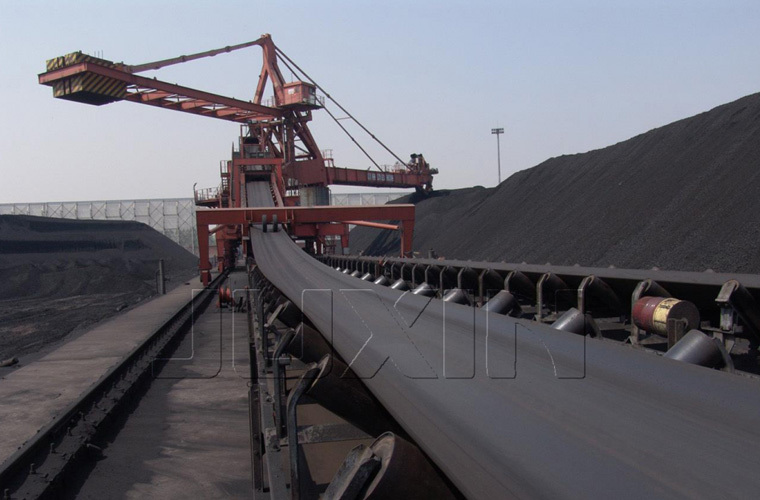
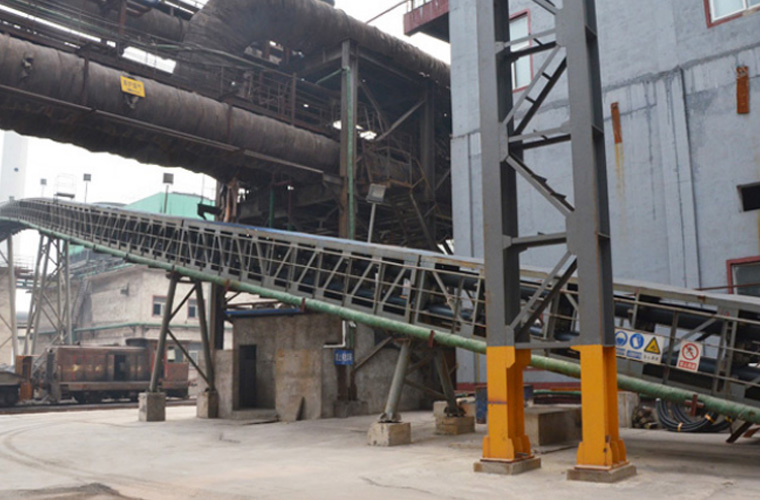
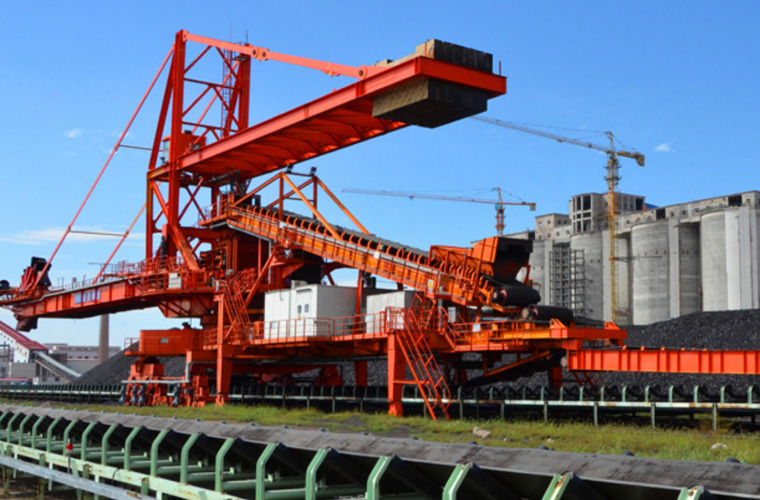
Previous:
Next:
Online inquiry